Under the leadership of Su Yongqiang, Shen Gu survived the most difficult stage in history and finally turned the corner.
In January 2006, at the national science and technology conference, the national leaders formally put forward the policy of "independent innovation". A month later, the State Council issued "Several Opinions on Accelerating the Revitalization of Equipment Manufacturing Industry" (the State Council No.8 Document in 2006), which proposed that "we should select a number of major technical equipment and products that have an important impact on national economic security and national defense construction, have a significant effect on promoting the sustainable development of the national economy, have a positive driving role in structural adjustment and industrial upgrading, and can expand the market share of independent equipment as soon as possible, and increase policy support and guidance to achieve major breakthroughs in key areas."
Among the 16 key breakthrough areas listed in this document, two are directly related to Shengu, namely, the localization of large-scale ethylene complete sets of equipment of one million tons and the research and development of large-scale coal chemical complete sets of equipment. The transformation of the country’s major policies has provided conditions for the all-round breakthrough of Shen Gu.
Text | Lu Feng Wang Chen Guo Nianshun Peking University School of Government Administration
Editor | Xie Fang looks at the think tank
In order to reprint the original articles of Wangzhi think tank, please indicate the source of Wangzhi think tank (zhczyj) and the author’s information before the article, otherwise the legal responsibility will be strictly investigated.
one
"Localization" has finally entered the room.
While China’s 300,000-ton ethylene equipment has not been made in China, the international ethylene equipment continues to develop to a large scale, and a million-ton ethylene plant was built in the second half of 1990s. After entering the 21st century, China has also built three million-ton ethylene projects with the international trend, namely, the 900,000-ton ethylene project of Shanghai Secco Petrochemical Co., Ltd., the 800,000-ton/year ethylene project of China Shipping Shell, the 10,000-ton oil refining project of Dushanzi Petrochemical Company of PetroChina and the 1,000-ton ethylene project. However, they all did not use domestic main equipment because of joint ventures and other reasons.
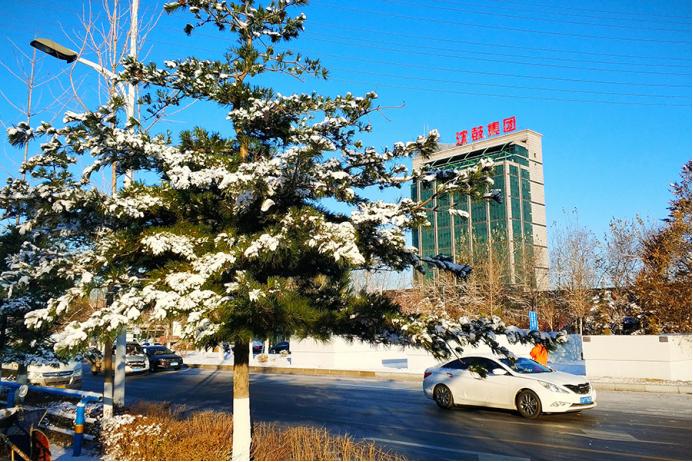
Shengu Group. Figure | Figure worm creativity
At that time, excessive dependence on imported equipment has become a stumbling block to the development of petrochemical industry in China. In a report to the National Development and Reform Commission, Sinopec wrote: "In recent years, the shortage of international special equipment and materials resources has brought great pressure on the supply of equipment in the domestic petrochemical industry. For example, the supply of large-scale units such as ethylene’ three machines’ (cracking gas compressor, propylene compressor and ethylene compressor) is very tight in the global market, and some foreign manufacturers often do not respond to domestic inquiries. The delivery time has been extended from 12 months in 2003 to 22-24 months in 2007, and the price has nearly doubled. "[1].
Obviously, if the equipment is not localized, the petrochemical industry in China, which has entered a high-growth track, will be curbed.
The first self-built million-ton ethylene project in China was the 1 million-ton/year ethylene reconstruction and expansion project of Maoming Petrochemical Company, which was formally started in December 2004 and completed in September 2006. It was based on the 360,000-ton/year ethylene project of Maoming Petrochemical Company. According to the report on the website of SASAC, "448 of the total 510 cracking units in the project are made in China, and the localization rate of the equipment is 87.8%. Not only the new technology of ethylene cracking and ethylene recovery jointly developed by China Petrochemical and Rhuems Company of the United States is adopted, but also some core equipment such as ethylene cracking gas compressor and cold box are localized." [2] The cracked gas compressor mentioned in this report is provided by Shen Gu, but at the enterprise level, the actual situation is not so "politically correct".
When Maoming Petrochemical signed a contract with Shen Gu, the venue ready for signing had been arranged. The boss in charge of technology of the other party took Su Yongqiang and said, let’s have a talk outside. Su Yongqiang asked him, "We have to sign this time. What’s your attitude now?" The other party said, "I still agree to import." When Sue asked why, he said, "Manager Su, you have to understand me. I know that you are capable and you can do well, but if you say it from my mouth, my head will be smashed." Most of the risks are understood, and the deeper reasons are not mentioned. You can sign if you have the ability, and I will serve you if you sign. " Su Yongqiang said he would sign it right away, but he still didn’t believe it. Of course, Su Yongqiang signed it-"Maybe I’m a competitive person, and I have to do what I can’t do."
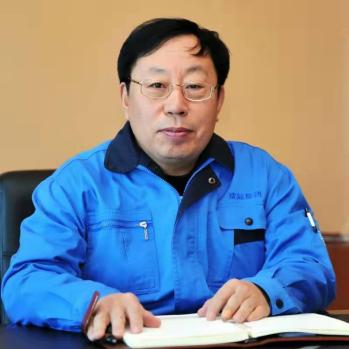
Su Yongqiang.
The major turning point of "localization" is the establishment of the national policy of independent innovation. In June, 2006, according to "Several Opinions on Accelerating the Revitalization of Equipment Manufacturing Industry", the million-ton large-scale ethylene complete equipment was listed as the key point of localization by the National Development and Reform Commission. At that time, the localization rate of ethylene plant, PTA complete sets of technical equipment and natural gas long-distance pipeline equipment was required to be not less than 75%.
In this context, China decided to invest 20 billion yuan in Tianjin, Zhenhai and Fushun to build three million-ton ethylene projects, and gave Shengu Group the task of supporting "three units". However, to be on the safe side, the million-ton ethylene "three machines" developed by Shengu for the first time were not put into the same project, but were respectively assigned to three million-ton ethylene plants, namely, Sinopec Tianjin Petrochemical used cracking gas compressor, Sinopec Zhenhai Refining and Chemical Company used propylene compressor, and Fushun Petrochemical Company under PetroChina used ethylene compressor.
When Su Yongqiang took the "Shangfang Sword" (that is, the task assigned by the government department) to find the main leaders of the party group of big users, they still said that it was best to ask Zhang Guobao, deputy director of the National Development and Reform Commission, to sign it. Su Yongqiang still remembers what Zhang Guobao said to him: Lao Su, I am the deputy director of the National Development and Reform Commission, and I have never signed for the enterprise. But you are special, and you are promoting localization. Although Deputy Director Zhang Guobao hesitated, he finally signed it on the spot. To put it bluntly, it is still risky, otherwise the project can be decided between enterprises.
People in petrochemical companies told Su Yongqiang that the value of one-time feeding of a million-ton ethylene plant is 160 million yuan. If there is something wrong with the "three machines" of ethylene, all the plants have to stop and all the raw materials of 160 million yuan have to be released. How many compressors do you have to buy? By May, 2007, all parties signed the contract, and Shengu Group began to undertake the research and development tasks of cracking gas compressor, propylene compressor and ethylene compressor of the million tons/year ethylene plant.
2
Break through the core technology again
In fact, Shen Gu has been preparing for the development of million-ton ethylene "three machines" for a long time, and has invested tens of millions of yuan in research and development expenses before getting the contract. Compressor is a customized large-scale complex product system. Without the application of specific engineering, it is of little significance to make an independent prototype. Therefore, Shen Gu’s product development is basically combined with engineering projects, that is, it is put into product development when there is an order. However, the research and development of related technologies for new products has actually started.
An important prerequisite for realizing large-scale equipment is the breakthrough of core technology. For the compressor with heavy drum, the first key technology is impeller. The large-scale compressor brings many practical problems: the reliability of large-size impeller operation, the quality problems caused by welding deformation, defects and thermal stress, and the corrosion of defective parts under bad working conditions.
In 2005, the R&D team headed by Cui Lianshun (female) began to develop the integral milling impeller that only GE mastered at that time. Integral milling impeller has attracted much attention because it is much better than welded impeller in material utilization rate, machining efficiency, machining quality and corrosion resistance, but the process of integral milling is very difficult. First of all, to process the general outline of the impeller on an extremely expensive low-temperature steel, even rough machining requires extremely fine requirements. The position of the first knife is particularly critical, and the whole blank may be scrapped if it is not careful. The tool used is a harder material than the billet, and the redundant part is removed one minute at a time during rotation. Then, this rough machined part is sent to the CNC milling machine for the most critical overall milling, and the straight cutter will mill spiral blades on this whole billet. This is an extremely complicated procedure, and the slightest error will make the whole project go to waste.
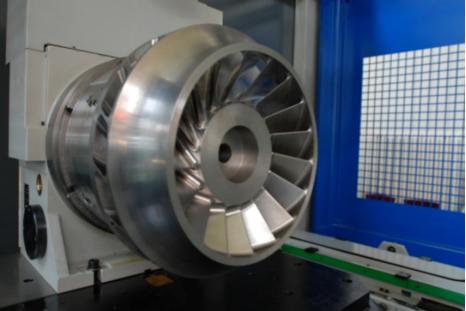
Integral milling impeller fixed on milling machine.
After two years’ efforts, Cui Lianshun’s team successfully developed a three-dimensional closed impeller with integral milling in May 2007, making Shengu one of the only two enterprises in the world to master this technology at that time. The maximum diameter of the impeller with integral milling is 1500mm(1.5 m), which has reached the advanced level in the world.
After 2007, Shengu continuously broke through the million-ton ethylene compressor, long-distance pipeline compressor and large air separation compressor because of the application of large-scale integral milling impeller technology. With this technology research and development as the foundation, Shengu has always maintained an outstanding record of "if you do it, you will succeed" in those large projects that adopt the first set of equipment.
three
The Battle of "Million Tons of Ethylene"
The foundation stone was laid in June 2006 for the million-ton ethylene project of Tianjin Petrochemical Company, and it was officially put into commercial operation in May 2010. The first million-ton cracked gas compressor developed by Shengu for this project was installed in June 2009. When this unit is appraised at the factory, the appraisal meeting will end in 20 minutes. Usually, this meeting will last at least two hours. Then why did it only last for 20 minutes? Because all the data displayed in the instrument are advanced, there is no question to ask after reading the report, and it will be passed directly.
Finally, the relevant leaders made a summary, saying that all indicators showed that this unit was an excellent one. He talked about an experience: after dealing with Shen Gu for so many years, our greatest experience is the enterprise characteristics of Shen Gu: as long as it is a difficult bone, a complex, risky and technically complex project, Shen Gu will certainly win it.
There is another episode. When this million-ton ethylene cracking gas compressor was tested in Shengu, Sinopec invited an expert from Mitsubishi Heavy Industries of Japan to verify it. This is because the only enterprise that can produce this kind of large centrifugal compressor in China is Shen Gu, so no experts other than Shen Gu can do third-party certification. Su Yongqiang was at the scene. Japanese experts carefully watched the whole experimental process of Shen Gu without saying a word, and looked at the data. After all the tests were finished, the leader of Sinopec asked the Japanese expert about his skills, but he still didn’t say anything, just raised his thumb-a world-class level.
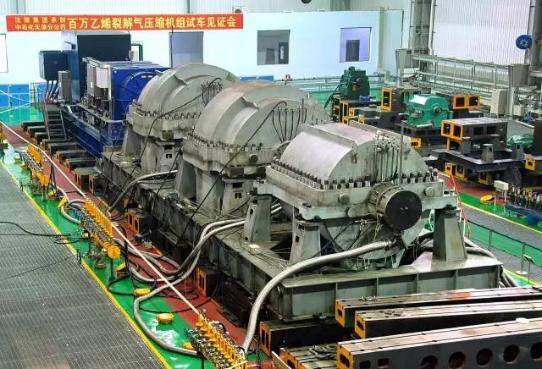
Shengu is the cracking gas compressor unit provided by Sinopec Tianjin Petrochemical Company for the million-ton ethylene project.
Sinopec Zhenhai Refining and Chemical Company’s 1 million tons/year ethylene project started in November 2006 and was completed and put into operation in April 2010. Shengu developed the first million-ton propylene compressor unit in China. Both propylene compressor and ethylene compressor are refrigeration, and their working environment is low temperature (propylene is generally used for refrigeration users at -50~0℃).
Zhenhai Refining & Chemical Company, as a user, requires that all partitions of Shengu compressor should be designed and manufactured with low-temperature resistant plates or forgings. In order to reduce the impeller diameter of the unit as a whole, Shengu adopted a high-efficiency three-dimensional impeller with large flow coefficient, high energy head and high Mach number, which was newly developed by R&D department and verified by performance experiments. Since then, Shengu propylene compressor unit has continuously passed the six levels of product design, large-scale casing assembly welding, impeller milling, rotor high-speed balance, mechanical operation test and performance test, and passed the factory acceptance of Sinopec Acceptance Committee in May 2009.
The acceptance experts agreed that the performance index of the propylene compressor unit in the million-ton ethylene plant reached the requirement of the technical agreement that the power deviation of the whole unit should not be greater than 2% of the design power, and the overall technical level reached the international advanced level, breaking the situation that this kind of products depended on imports for a long time.
The ethylene compressor is the last breakthrough in the development of ethylene "three machines" in Shengu. Ethylene compressors are generally used for users of cryogenic separation (-102~-60℃), and Shen Gu didn’t wait until 2006 to develop ethylene compressors for the first time. At that time, Huajin Group in Panjin handed over the order of ethylene compressors for the 450,000-ton/year ethylene expansion project to Shen Gu.
The leading designer of this project is Jiang Yan, a female engineer born in 1973. Without this kind of compressor development experience and external technical knowledge sources, Jiang Yan team worked hard and put in 3 years’ efforts to produce the products. However, this unit, which was put into trial operation in the factory, encountered the problem of excessive vibration as soon as the production line of Huajin was turned on. The reason is that the operating condition of the factory is normal temperature, but it is ultra-low temperature when it is turned on. Jiang Yan and the team searched for technical defects one by one, and finally broke the core problem of rotor structure operating at ultra-low temperature, and realized the stable operation of the first domestic ethylene compressor on January 8, 2010.
The 800,000-ton/a ethylene plant of Fushun Petrochemical Company started construction in April 2009, and the design task of developing the first million-ton ethylene compressor in China by Shengu was also given to Jiang Yan. In this project, Jiang Yan once again showed the courage and creativity of the Shen Gu technical team who dared to go their own way.
The structure and manufacturing process of large-scale ethylene compressor are very different from those of conventional compressors, and the biggest technical problem is the gas charging structure. In order to improve the efficiency of the general compressor, when it is compressed to a certain temperature by several stages of impellers, the compressed medium must be cooled and then compressed. Jiang Yan thinks that if the million-ton ethylene compressor is designed according to this method, it is necessary to add multiple air ducts, which will inevitably divide one compressor into two, resulting in double cost and reduced efficiency.
During that time, Jiang Yan couldn’t eat or sleep, and his mind was full of gas flow field maps. By chance, a sample of a low-temperature rotor detonated her idea: isn’t ethylene at MINUS 100 degrees Celsius itself a refrigeration medium? There is no need to toss the gas inside and out at such a low temperature. After asking for instructions, she decided to adopt the method of filling gas in the cylinder in the million-ton ethylene compressor. However, it is a major change in the structure of the whole unit from adding gas into the cylinder to adding gas into the cylinder. How to optimize the gas flow field without external gas addition, make the two gas additions not interfere with each other, improve efficiency and reduce the difficulty of casing processing, etc., involves the whole production process such as design, technology, processing and manufacturing. And all these problems, Jiang Yan must be solved one by one in the design process of product production source.
Jiang Yan has been cornered many times, and it often took days and nights to design the structure, but it was rejected because of a small defect. However, she and her team didn’t give up. When a structure was rejected, they carefully studied what they could learn from and applied it to the next scheme. In this way, with little accumulation and little improvement, Jiang Yan team perfected the structural design scheme of the unit in constant self-denial. At the same time, they have done a lot of basic research, from rotor dynamics to fluid mechanics to model-level development, constantly calculating every detail of simulating gas flow. After repeated argumentation and simulation, they finally formed a perfect design scheme for filling gas in the compressor cylinder. Practice has proved that the in-cylinder aerated structure greatly improves the performance and efficiency of the product, which is better than foreign units in some aspects [3].
The ethylene compressor should not only meet the strength requirements of the machine, but also improve the efficiency. By optimizing the design of the rotating parts such as the impeller, the Jiang Yan team successively overcame the difficulties such as the rotor structure, and finally formed a perfect design scheme for the million-ton ethylene compressor.
On the evening of February 22nd, 2011, the first million-ton ethylene compressor set in China was successfully tested in the assembly workshop of Shengu Group. In October 2012, Fushun Petrochemical’s 800,000-ton ethylene production plant was completed and put into operation. Since then, Shengu Group has successively signed several large-scale ethylene projects such as Wuhan, Yanshan, Huanggang and Zhenhai, and Jiang Yan team has designed and manufactured 16 ethylene compressor units in three years.
With the continuous success in developing the first set of equipment, Shen Gu is more and more trusted by users. In August, 2011, Sinopec Group and its affiliated Wuhan Branch packaged the products at one time, and delivered the orders for 8 centrifugal compressor sets, 5 reciprocating compressor sets and 4 pumps for the 800,000-ton/a ethylene project in Wuhan to Shengu. The total contract amount exceeded 300 million yuan, including the complete design and manufacture of all ethylene "three machines".
In 2013, Sinopec Wuhan 800,000-ton ethylene project was completed and put into operation. For the first time, Shengu became the general contractor of the million-ton ethylene "three machines". This is a great success, which proves that Shengu has become the mainstream supplier of ethylene "three machines".
In July 2013, the second phase of CNOOC Huizhou Refining and Chemical Company started construction, which is a project to build 10 million tons/year oil refining and 1 million tons/year ethylene on the basis of the first phase of 12 million tons/year oil refining, and it is also the first refinery in the world to centrally process heavy crude oil with high acid content. Its 1.2 million tons/year ethylene production facility was the largest in China and the most advanced in the world at that time [4]. In September 2014, CNOOC signed a contract with Shengu to provide all ethylene "three machines" for Huizhou Refinery Phase II project. In April 2018, CNOOC Huizhou Refinery’s 1.2 million tons/year ethylene plant produced qualified propylene and ethylene products.
So far, Shengu has become one of the top compressor manufacturers in the world.
Zhongsha (Tianjin) Petrochemical Co., Ltd. (formerly Sinopec Tianjin Petrochemical Co., Ltd.) decided to expand its capacity after 10 years of operation of its million-ton ethylene plant. In July, 2020, the nitrogen test run of the cracking gas compressor unit of the largest domestic ethylene plant with a capacity of 1.3 million tons/year, which was installed by Shengu Group, was successful once, and the mechanical performance parameters of the unit reached the high-quality level. The successful commissioning of the unit modification indicates that Shengu Group has been in the leading position in the world in the research, modification and installation of the million-ton ethylene compressor unit.
"Localization" is an important reason why China has made great progress in ethylene production: during the 30 years from 1975 to 2005, China’s annual ethylene production reached 6 million tons, and in the 15 years since the breakthrough of domestic equipment, China’s annual ethylene production reached about 21.6 million tons, and China became the second largest ethylene producer in the world after the United States.
Figure: Ethylene production in China from 1970 to 2020 (thousand tons)
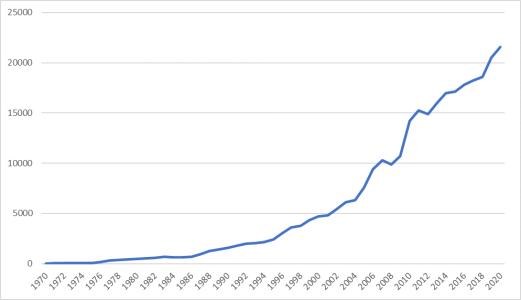
Source: National Bureau of Statistics.
four
The Battle of "Long-distance Pipeline"
After the compressor of large-scale ethylene plant, another "localization" campaign of Shengu is the long-distance natural gas pipeline compressor, which should start from the "West-East Gas Transmission Project".
In February 2000, the first meeting in the State Council approved the start of the "West-to-East Gas Transmission Project", which is a great project in China’s energy field and the largest national project after the Three Gorges. Up to now, the "West-East Gas Transmission Project" has been divided into three stages, namely, West Line 1, West Line 2 and West Line 3. The general situation is as follows.
The West First Line Project was officially started in July 2002, passing through major provincial administrative regions such as Xinjiang-Gansu-Ningxia-Shaanxi-Shanxi-Henan-Anhui-Jiangsu-Shanghai, and was completed in 2004.
The West Second Line Project started in 2009, passing through major provincial administrative regions such as Xinjiang-Gansu-Ningxia-Shaanxi-Henan-Hubei-Jiangxi-Guangdong, and was completed and put into operation by the end of 2012. The West Second Line is the longest pipeline in China so far, with the highest pipeline steel grade, the largest pipe diameter, the largest gas transmission capacity and the greatest energy saving and emission reduction effect. The trunk line and branch line are all over 8,700 kilometers long, and the natural gas transported has entered the Yangtze River Delta and Pearl River Delta regions along the southeast coast through 15 provinces (autonomous regions and municipalities). If we add the foreign Central Asian natural gas pipeline, it can be said to be an "underground Great Wall of Wan Li Pipeline".
The West Third Line Project started in October 2012. The trunk and branch lines pass through 10 provinces and autonomous regions in Xinjiang-Gansu-Ningxia-Shaanxi-Henan-Hubei-Hunan-Jiangxi-Fujian-Guangdong. The total length of trunk lines and branch lines is 7,378 kilometers, which was completed in August 2014.
However, at the beginning of the "West-to-East Gas Transmission Project", it was also a major project relying on imported equipment. The pipeline of "west-to-east gas transmission" needs a lot of equipment, and the compressor is one of the key equipment, and it is the most important key equipment. The flow of natural gas in the pipeline depends on the power provided by the compressor, so it is necessary to build a pressurizing station every 200 kilometers and pressurize it with the compressor. The key equipment, including compressors, of the West First Line Project are all imported, and almost all of the West Second Line Project are imported. However, the only foreign enterprises that can provide pipeline gas compressors are GE, Rolls-Royce and Siemens.
Sui Yongbin, the chief engineer and consultant of China Machinery Industry Federation, was once the deputy director of the Ministry of Machinery Industry, and he was a man of lofty ideals who campaigned for the localization of major technical equipment for decades. According to his explanation: "The localization of China gas pipeline should not start from now. In the 1970s, the idea of "Sichuan gas flowing out of Sichuan" was put forward. In order to cooperate with "Sichuan gas flowing out of Sichuan", Chinese equipment manufacturers began to develop pipeline ball valves and compressors, and developed gas starters to drive pipeline compressors. For various reasons, the project was finally terminated. "
China decided to launch the "West-to-East Gas Transmission Project", which once again brought opportunities to China equipment enterprises. In Sui Yongbin’s words, "domestic equipment manufacturers have been waiting for opportunities since the beginning of the construction of the first line of the West-to-East Gas Transmission Project, hoping that the key equipment of the long-distance natural gas pipeline in China can use domestic equipment" [5].
However, this wait is nine years.
Shen Gu has been tracking since 1999, when the country was brewing the "West-to-East Gas Transmission Project". Since the first demonstration meeting of localization, Su Yongqiang has participated in 14 of the 16 demonstration meetings, and made speeches at the meeting every time, arguing with arguments, but failed to win a project.
The argument of west-to-east gas transmission is soul-stirring. Sometimes, people from Shen Gu didn’t get a chance to speak at the meeting, so the meeting decided to import it, and we will mention it domestically next time. Before this, Shen Gu did not make a gas pipeline compressor, but this kind of machinery is not complicated from principle to manufacture, and there is no insurmountable technical obstacle for Shen Gu. The problem is not technology-if domestic equipment is used, once problems occur, 500 million people will have no food. Who will bear the risk? Once the compressor is started, it will keep running for 365 days a year, and once an accident occurs, it will affect the overall situation.
[Note: The compressor unit used to be overhauled after 8000 hours of operation, but it was extended to one and a half years, then three years, and now it is overhauled every five years. 】
Even with heavy resistance, Shen Gu has been preparing for entering the long-distance pipeline market. In 2006, Shengu won the contract for the first "cooperative production" compressor, which was designed by GE and manufactured by Shengu. In 2007, I got a prototype, all designed and assembled by Shen Gu, but the prime mover (motor) and frequency converter were bought from abroad, and finally three finished products were made. Although Shen Gu failed to win an order for his compressor, when the country held a commendation meeting for the West-East Gas Pipeline Project, it still commended Shen Gu as an advanced unit and gave Su Yongqiang an outstanding individual. The award was signed by the the State Council West-East Gas Pipeline Leading Group.
Su Yongqiang asked the leaders of the National Development and Reform Commission, who presided over the meeting, how could we be awarded advanced without providing a single unit? The leader’s answer is: users said that although they didn’t give Shen Gu an order, Shen Gu’s intervention allowed them to beat foreigners with Shen Gu and saved them old money, so Shen Gu made great contributions to the country. Su Yongqiang said, "If you want to say so, I deserve it."
The substantial progress of "localization" of the "West-to-East Gas Transmission Project" occurred at the beginning of the construction of the West Second Line.
In April, 2009, the National Energy Administration held a meeting on "Localization of Key Equipment of Natural Gas Long-distance Pipeline" in Shenyang, and decided to carry out the localization research and development of "20MW electric drive compressor set", "30MW gas drive compressor set" and "high-pressure large-diameter welded ball valve" for the West Second Line Project.
Under the organization and coordination of the National Energy Administration, PetroChina took the lead in name, and Shengu developed a 20MW electric drive compressor unit, CSIC 703 developed a 30MW electric drive compressor unit, Shanghai Electric Group and Harbin Electric Group made motors, Anshan Rongxin Electric Power and SVA made frequency conversion, and five companies formed a company. In July 2010, the high-pressure large-caliber welded ball valve was successfully developed in Chengdu; In November, 2011, 20MW electric drive compressor set was successfully developed in Shengu. So far, the key technologies and equipment that restrict the long-distance natural gas pipeline in China have been successfully developed.
PetroChina paid experts from GE to certify the prototype of Shengu, and the result was excellent. Someone at the scene deliberately "provoked" and asked the experts of GE: What do you think of the comparison with the GE unit? The foreign expert replied that everything was fine, and even he was happy when he said it-in fact, he knew that the index of Shengu unit was better than GE.
However, although the policy of "localization" has been decided at the government level, and even domestic equipment has begun to be developed, there are still many obstacles to adopting domestic equipment at the implementation level. During the two years from 2009 to 2011, the debate on whether to adopt domestic equipment in the West Second Line Project has been in a state of "tug-of-war": it was approved at this meeting and overturned next time; After another meeting, it was decided to make it in China, and it was overthrown next time …
After several round trips, Sui Yongbin proposed to plan a cartoon, and Su Yongqiang found a professor from Shenyang Luxun Academy of Fine Arts to draw it. The professor drew several editions and passed them on to Sui Yongbin. Sui said that the painting was wrong and did not reach the artistic conception. Su Yongqiang discussed with Professor Lumei again, explaining to him that this is like tug-of-war, which is related to whether you win or I win.
In the final version, a tug-of-war competition was designed. On one side, there were three foreigners, Siemens, Rollo and GE, and on the other side, there were a bunch of Chinese cheerleaders, with Sui Yongbin and Su Yongqiang at the head. Su Yongqiang said, "I’m the little fat guy on the side, and I look quite like him." The referee in the middle was PetroChina, to see who won, so he finally sided with Chinese. Sui Yongbin is satisfied with this cartoon. At the last demonstration meeting, Sui Yongbin couldn’t speak at that time, so he went up to tell the cartoon himself. Then each enterprise spoke, and as a result, opinions were still inconsistent during the break.
At the end of the meeting, the senior vice president of PetroChina came forward. Before making his final statement, he called Su Yongqiang and Sui Yongbin and said: You all know the responsibility of this matter, and you also know the reason why they don’t agree to adopt domestic equipment. It is that the risk is too great, not only economic risk, but also political risk. If something goes wrong, this job will be lost. He asked Su Yongqiang directly: Do you have confidence? Su Yongqiang said yes. Later, when the meeting resumed, the vice president spoke passionately about the fact that central enterprises must take responsibility, bear national responsibility and support the localization of equipment, which was quite exciting. Finally, the parties decided to sign.
In 2012, the first pipeline compressor independently developed by Shengu was installed as a backup machine in Gaoling pressurization station of the West Second Line. But no one expected that a dramatic scene would happen later: the foreign compressor as the main engine could not be started after maintenance, so it had to start the standby drum sinking unit urgently, and the drum sinking unit was successfully started at one time. This accident made the standby machine of Shen Gu instantly become the host machine.
Since then, the National Energy Administration has organized a national appraisal in Gaoling, and the pipeline compressor of Shengu has received three evaluations: first, the performance has all met the design requirements, and compared with foreign units, it is truly world-class; Second, the fastest driving speed, a successful driving, and foreign units can not do, it will take a long time to drive; Thirdly, the most surprising thing is that the noise of Shengu unit is much lower than that of foreign units. When Su Yongqiang went to the scene, the people who used the unit told him that the Shen Gu unit was so good that after the foreign unit was driven, the people at the scene could not hear each other, but they could hear each other when the Shen Gu unit was running. Shen Gu people never thought that their compressor had this advantage. Su Yongqiang said, in fact, as soon as the mechanical and pneumatic indicators are reached, the noise will naturally come down, so the low noise just shows that the technical performance of the Shen-Gu compressor is excellent.
Shengu’s long-distance pipeline compressor was a hit at Gaoling pressurization station in the later period of the second line project of "West-to-East Gas Transmission" and was highly appraised. At present, there are a few imported compressors driven by gas turbine, and all the electric-driven compressors have been made in China (the number of electric-driven compressors exceeds that of gas-driven compressors). In other words, the compressors used in the first line of the "West-to-East Gas Transmission Project" are 100% imported, and almost all the compressors used in the second line are imported. Up to then, about 300 compressors have been imported into the "West-to-East Gas Transmission Project", and a rough calculation has cost about 30 billion yuan, of which the tax revenue, profits, employment and experience accumulated do not belong to China.
Since 2009, Shengu has independently developed the electric-driven compressor for long-distance pipelines, made a prototype in 2011 and installed it on the spot in 2012 (since then, CSIC 703 has successfully developed a gas-driven pipeline compressor). Since the Shengu compressor was launched at Gaoling Station of the West Second Line, there is no imported pipeline compressor driven by electricity, and the West Third Line has been localized.
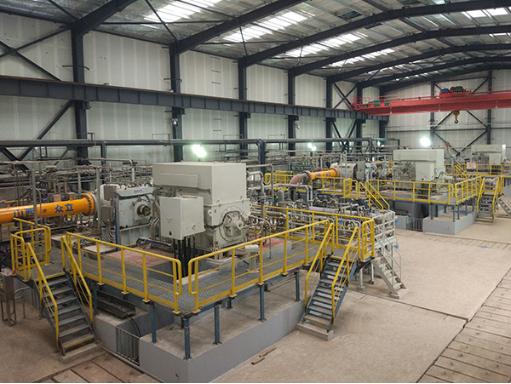
On June 26, 2017, three sets of PCL compressor units provided by Shengu Group for Sinopec’s "Sichuan-East Gas Transmission Project" gold station completed 72-hour commissioning test on site, and all indicators were normal and met the design requirements.
On December 28th, 2021, the annual gas transmission capacity of the West-to-East Gas Pipeline System, a landmark project of China’s western development, exceeded 100 billion cubic meters that day. The important reason for this achievement is that in 2018, the country implemented the natural gas pipeline interconnection and supply guarantee project, and Shengu Group provided 14 sets of compressors for this project, which were all put into production in January 2019. In December, 2020, the East Line Project of Sino-Russian Natural Gas Pipeline (Changling-Yongqing) was successfully put into operation, and Shengu provided the design, manufacture and on-site service of 15 compressor sets in 5 stations for this project.
five
Battle of "100,000 air separation"
When the country implemented the policy of adjusting the energy structure around 2010, the intensive processing of China’s rich coal resources (such as coal to oil, coal to natural gas, coal to olefins, coal to aromatics, etc.) required larger-scale air separation compressors. At that time, in the world, only two German companies, Siemens and Man Turbine, could produce the 100,000-class air separation compressor units needed by large-scale coal chemical plants, and China could only rely on imports.
However, for the competent authorities, the prospect of developing coal chemical industry entirely by imported equipment is "horrible": a set of 4 million tons/year coal indirect liquefaction oil-making device needs to produce 1.2 million Nm?3 oxygen; /Hr air separation island and 12 sets of air compressors with 100,000 air separation (oxygen production). By 2015, more than 70 sets of air separation compressors of this scale will be needed for coal chemical projects approved and to be approved by the state.
In October, 2011, the National Energy Administration organized a working conference on the localization of key equipment of Shenhua Ningmei’s 4 million tons/year coal indirect liquefaction project, and proposed that localization must be carried out. In 2013, of the 12 sets of 100,000 air separation units required for this project, 6 sets were acquired by Hangzhou Oxygen Machine Group (hereinafter referred to as "Hangzhou Oxygen"). After expert argumentation, the National Energy Administration decided to set aside one of the 12 compressor units originally planned to be imported for the air separation unit in Shenhua Ningmei Project as a pilot for localization, and requested Shengu to carry out the research and development of 100,000 air separation compressor units.
This is another challenging task: the design and production cycle of the compressor is one and a half years, and the on-site installation takes half a year, which adds up to a two-year cycle; If it is not successful at one time, the redevelopment will lose four years, and the whole project with an investment of tens of billions of yuan will have to wait. Therefore, Shen Gu must be successful once, which is the most difficult part of "localization".
Shenhua Ningmei planned to import 100,000 air separation compressors at that time, each of which needed 150 million yuan. After the news of Shen Gu’s "localization" came out, the compressor price of foreign enterprises immediately dropped to about 100 million yuan.
The cause and effect of this project once again shows the logic of the "localization" model: major projects to be built in China must use major technical equipment that has not been developed and manufactured in China, but it is at least financially infeasible to rely entirely on imported equipment. Therefore, the government put forward the "localization" policy for the purpose of reducing the cost of using advanced technical equipment and gave China enterprises market opportunities.
However, this time there is a fundamental difference-because Shen Gu is not the same. The key to understanding the road of Shengu lies in this: after entering the 21st century, every time Shengu completed the task of "localization", it did not copy the imported foreign compressor technology, but replaced the foreign compressor with a self-developed compressor.
In fact, Shen Gu has been preparing for this opportunity for many years. Shengu Group has been committed to the development of compressors for large-scale air separation units since 2002, and successfully delivered the first set of 40,000 air separation compressors in China to users in 2004. In the same year, under the condition of no contract, Shengu completed the manufacture and test of a prototype of 35,000 gear-assembled air compressor units by self-financing. In 2006, Shengu developed the first set of 52,000 air separation compressor units in China, which was successfully started after being delivered to users. In 2010, the Energy Bureau of the National Development and Reform Commission determined that Shengu Group was the only R&D center for large turbocompressors in China. In the same year, Shengu completed the research and development design of 50,000 multi-shaft and multi-stage gear assembled air separation booster unit by self-financing, and completed the manufacturing and testing work in 2012, which solved the technical problems of high-efficiency impeller model stage, rotor stability, core component materials and strength analysis, and completed the test verification of more than 20 independent research and development new technologies.
After accepting the task, Shen Gu designated the "Development Project of Compressor Unit Supporting 100,000-class Air Separation Equipment" as "Pioneer Project of Communist party member". Su Yongqiang, the chairman of the board of directors, is personally in charge, Dai Jishuang, the deputy general manager, is responsible for the implementation, and the chief designer of the project is Wang Chuanghua, the vice president of the battle-hardened design institute.
As it is another "first set" project, the technical team of Shengu has no experience to learn from, whether it is the structural design of compressors and superchargers, seals and shells. However, they rely on mature large-scale centrifugal compressor technology and large-scale axial compressor technology, and adopt the structural design of "axial+centrifugal" air compressor and multi-shaft and multi-stage gear assembled supercharger in the R&D and design process. They have successively overcome a series of technical problems, such as high-efficiency impeller design with large hub ratio mixed flow and small hub ratio and high Mach number, cooperative coupling of various complex flows, dynamic analysis of rotor with special structure, complex connection structure of rotor and stator, complete set design of unit equipment, control and adjustment of complex working conditions and so on.
In order to hand in the best technical solutions to users, they constantly communicate with Hangyang Group and users to ensure the accuracy of each parameter, and also cooperate with foreign enterprises in individual technical fields to ensure the advanced nature of various technologies.
In August 2013, Shengu won the trust and recognition of experts and users with its technical scheme and service concept, and signed a commercial contract with Hangzhou Oxygen Group (air separation unit) and Hangzhou Steam Turbine Group (supporting steam turbine) for Shenhua Ningmei super-large air separation unit.
The manufacturing process is also a challenge. In the rotor workshop, the compressor spindle, which weighs nearly 30 tons, needs to be combined horizontally in three stages, and it needs to be successful once. There is only a gap of 0.02-0.04mm between the left and right sections of the spindle and the middle section, which is equivalent to one tenth of the hair. A slight negligence in installation will give up all previous efforts. On average, the 44 bolts on the left and right sides of the spindle have to be hammered more than 800 times and stretched more than 1000 times by workers. The rotor length of the air compressor in the 100,000 air separation project is 76.6 meters, which requires more than 300 people to repeatedly scrutinize the safety of the tooling, equipment and site. Each impeller has a weight of one ton, so the operator should wear a safety belt and stand on the assembly frame more than 7 meters high to operate.
In the stator workshop, the processing technology of the central casing is complex, and the same process involves the coordinated operation of multiple teams. According to the product structure characteristics and process flow, the workshop worked out a special production plan for the central casing of the 100,000 air separation project, and decomposed the plan into each process, strictly controlled the planned time nodes, kept track of the production progress at all times, and rationally arranged personnel, and each link was taken care of by a special person, so as to ensure the seamless docking of all teams and groups and ensure the production and processing were foolproof.
In the structural workshop, Nie Wanlong, who has provided technical services for the group’s heavy and difficult products for many times, was selected as the technical "chief surgeon" from the pre-production technical preparation. After receiving the drawings of 100,000 air separation units, Nie Wanlong immediately carefully analyzed the rationality of each process link and possible problems, and communicated with the design, process and other departments to solve the problems one by one. Subsequently, this heavy baton in Nie Wanlong’s hand was passed to the "Shenyang Welding King"-the technician Zhen Bide. Zhen Bide never let go of any problem, keeping a close eye on the production of 100,000 air separation units, and working overtime every day has become a common practice.
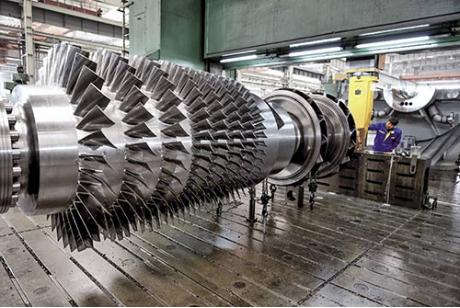
Rotor of 100,000 air separation compressor.
The development of large-scale equipment, especially the first set of equipment, requires large-scale test means. The power of large-scale air compressor set for 100,000 air separation plant exceeds 60,000 kilowatts, so it is very difficult to design and manufacture. In order to ensure that the development of the unit is foolproof, the product must be tested at full speed, full pressure and full load before leaving the factory. In 2012, Shengu invested 700 million yuan to build a world-leading 100,000 kW test bench in Yingkou, which was approved by the National Energy Administration as the national "Construction Project of R&D (Experiment) Center for Large Turbine Compressor Units". According to the actual operating parameters of users, the test-bed can test all the equipment including compressor, turbine, auxiliary machine, control system and so on.
From July 23rd to August 3rd, 2015, the 100,000 air separation compressor unit independently developed by the R&D teams of Shengu Group, Hangzhou Steam Turbine Group and Hangzhou Oxygen Group has successfully carried out the performance tests of mechanical performance and aerodynamic performance at full speed and full pressure for three times, and all the performance indexes meet the requirements of the contract and reach the international advanced level. Soon after, on August 23rd, 100,000 Nm?3 with a length of 35 meters, a height of 15 meters and a weight of 478 tons; /h The air separation compressor unit was commissioned at Shengu Yingkou Experimental Base, and conquered more than 200 guests including leaders, experts and customers with excellent performance.
On May 15th, 2017, the first domestic air compressor set of 100,000-class air separation plant independently developed by Shengu Group was successfully commissioned, and the linkage test of No.12 air separation unit of Shenhua Ningmei coal indirect liquefaction demonstration project was successfully completed. The operation data showed that all mechanical properties and aerodynamic performance indexes of the unit reached the international advanced level. On July 11, 2017, this compressor unit was connected to the grid and produced qualified oxygen and nitrogen products. The oxygen and nitrogen quality indicators met the design requirements and the mechanical properties of the unit were stable. The user Shenhua Ningmei specially sent a happy news to pay tribute to all the staff of Shengu Project Department and awarded the honorary title of excellent supplier of Shengu Turbine Company’s coal-to-liquid project.
On August 25, 2017, China Machinery Industry Federation and China General Machinery Industry Association jointly hosted a demonstration project of 4 million tons/year coal indirect liquefaction in Shenhua Ningmei-an industrial operation review meeting of domestic 100,000 air separation units and air compressors. The final evaluation opinion proves that the domestic 100,000-unit air separation plant and air compressor are another breakthrough of major equipment in China, and their main technical performance has reached the advanced level of similar foreign plants and products, which can meet the needs of large-scale domestic coal chemical, petrochemical and metallurgical projects for 100,000-level and above air separation plants. It is recommended to popularize them as soon as possible.
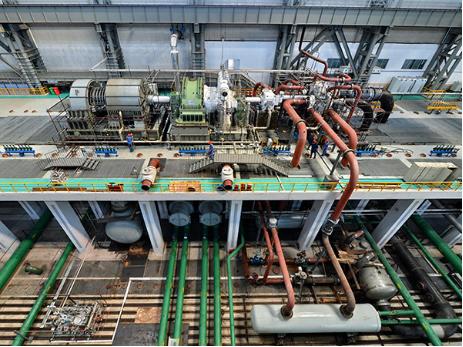
The whole picture of the first 100,000 air separation compressor set in China manufactured by Shengu, Shenhua Ningmei site. (Source: Shen Gu official website)
The 100,000 air separation compressor unit is a major breakthrough of Shengu in recent years. From the process, the whole process of "localization" is relatively smooth due to the direct intervention of the state authorities. This also shows that the market of major projects is deeply influenced by the government, and the role of the government in promoting "localization" at the "system" level is irreplaceable.
Following the breakthrough of Shenhua Ningmei Project, Shengu received contracts from two other enterprises in succession. In April 2020, Shengu Group designed and manufactured two sets of 105,000 air separation compressor units for Ningxia Baofeng Energy Group, and produced qualified oxygen and nitrogen products. This is another major breakthrough in the development of large-scale air separation units in China after the successful start-up of 100,000 air separation units developed for Shenhua Ningmei in May 2017.
On the basis of accumulating several sets of design and manufacturing experience of compressor units in large-scale air separation units, Shen Gu has successively developed 60,000, 80,000, 100,000, 120,000 and 150,000 Nm?3; Independent research and development of large air separation units with /h class, with 60,000 to 150,000 Nm?3; The design and manufacturing capacity of serial centrifugal compressor sets for /h air separation units shows the prospect of a full range of domestic compressor sets for large-scale air separation units replacing imports in the field of large-scale coal chemical industry.
The technical and product breakthroughs of Shen Gu in the last 20 years can’t come together, so we can only describe the general situation. Importantly, Shengu’s products have covered the upstream, midstream and downstream of petrochemical industry, and have rushed to the forefront of the world in almost all fields, which is a great contribution made by Shengu to China’s industry. In addition to the aforementioned fields of ethylene and natural gas long-distance pipelines and coal chemical industry, the technical breakthrough of Shengu also includes the following fields: compressors for oil production and oil refining, compressors for natural gas liquefaction (LNG) refrigerants, compressors for fertilizer production devices, and compressors for chemical fiber production devices. In addition, Shengu also provides high-end pumps, such as nuclear power plant main pump and oil pipeline pump.
It can be said that Shengu has fully covered the large-scale compressor units needed by petrochemical industry, national defense and military industry, and its market share is roughly as follows: centrifugal compressor is 85%; Large blowers account for 40%; The reciprocating compressor in petrochemical industry is about 80%; High-end pumps range from 50% to 85% according to the variety.
It is precisely because Shengu quickly realized the large-scale compressor, the improvement of technical level and the enhancement of supporting capacity that it met the development of petrochemical industry in China in the past 20 years. The president-level leader of a big user personally said to Su Yongqiang: "Mr. Su, Shen Gu has made great contributions to the development of China petrochemical industry. Your contribution to the country should be measured not by how much profit Shen Gu has produced, but by the social contribution you have made to the country. With Shen Gu, we dare to say no in front of foreigners. "
Notes:
[1] The story behind Sinopec’s promotion of ethylene plant localization | Pang Hongming, Gas Separation, No.2, 2010, p.25.
[2] China’s first million-ton ethylene production base has been fully completed and put into operation | SASAC website, September 19, 2006
[3] Jiang Yan dictated: "Little Ben" designed the world’s top equipment | "Contemporary Model Workers", No.10, 2013, pp. 53-55.
[4] On December 15th, 2015, Dutch Shell Group and CNOOC signed the Agreement on Major Terms for Enhancing Cooperation in Daya Bay, and Shell Company participated in the construction and operation of the 1,000,000-ton/year ethylene plant in the second phase of CNOOC Huizhou Refining and Chemical Project.
[5] High-end equipment casts an energy artery —— Three "Forever" arguments on the localization process of the 20 MW electric drive compressor unit in the west-east gas pipeline | China Equipment, No.12, 2012, pp. 42-47.
Original title: "All-round Breakthrough of Localization"
Read the original text